Hi Marek,
I used Koi's file to have the profile he has made.
I made a boolean union to have a single profile.
I rebuild the curve to avoid the problems I could have with small edges next.
Now this is a seamless curve.
I extrude it to have a first solid. This solid is flat.
Next, I made the two red curves to do the flow by curves process.
for the non linear red curve, I made it with three lines joined.
I filleted the result and moved the points to have non symetrical fillet. This looks more realistic bending of metal.
With the first solid I flow it using the two red curves.
It gave me the second solid.
I use the same process to do a third solid using the second solid and the pink curves (curves made with the same method on the other axis)
I have redone it and I post the file here.
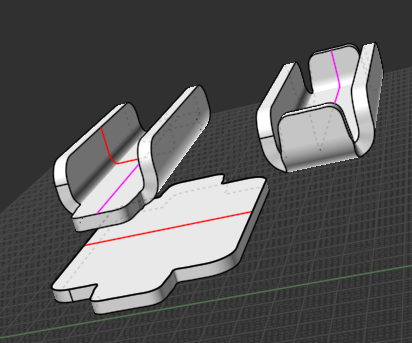
|